Talking about bicycles, especially those designed for extreme speeds, it comes natural to discuss about chains and pinions.
The transmission has to be studied carefully in order to waste as little watts as possible because of friction losses. The saved power can be then used to push the bike faster!
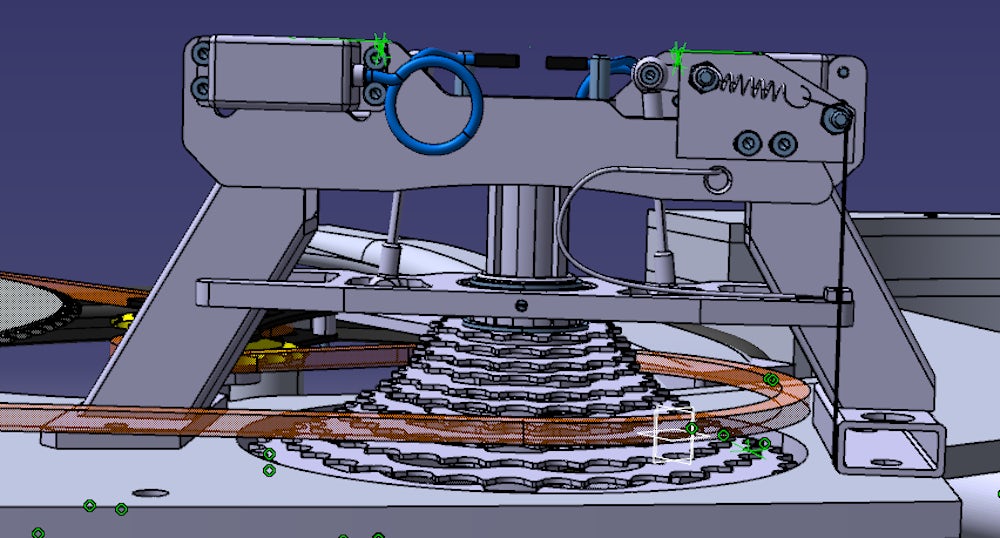
The need to make a more efficient transmission took place in 2017 with the introduction of Taurus. The reduced dimensions of the prototype made it very difficult to have a rear drive wheel, like we had with Pulsar, our previous bike. We decided to work on the front wheel.
This option usually leads to a limitation on the number of gears due to excessive misalignment of the chain caused by the short distance between the transmission axes. One way to solve this problem could have been using two chainrings combined to a 7-8 pinions cassette but, after discussing it, we opted for a moving cassette transmission.
The concept was not new, hence we were confident it would yield reliable and functional results. Therefore, we decided to focus on development of this design.
This type of transmission keeps the overall efficiency high forcing the chain to work on a plane parallel to the pinion’s one, this yields optimal power transfer conditions.
Moreover, we can implement as many pinion as we need, limited only by the available space. No matter how many speeds we put on, the chain will never risk derailing to unwanted gears or working badly due to the excessive misalignment of the transmission pinions.
The transmission V1.0
The system is made of two chains mounted on both sides of the bike frame connected by a transmission shaft. On the right side of the bike there is an impressive 108 teeth chainring. It is mounted on a power meter that can measure different values such as power and pedaling cadence. The chainring is connected to the 11v cassette by a chain that, as mentioned above, can move on the splined shaft (the cassette range goes between 13 and 40 teeth).
The pinions move axially, while allowing the torque to be transferred. The splined shaft is made of steal while the sleeve sliding on the shaft is bronze thus reducing the force required to move it.
The transmission shaft is fixed to the frame by two hybrid ball bearings: one is mounted on the left panel of the frame while the other is backed by a welded aluminum structure that also backs the servos for the moving action.
At this point, the torque is passed to a fixed chainring on the left side of the bike that, thanks to a second chain, is transmitted to the freewheel mounted on the axle of the front wheel. Both chains have their own tensioner made of carbon fiber to reduce weight. The tensioners mount machined aluminum pulleys which have their dedicated hybrid ball bearings. The left tensioner has a curved shape which helps with the maintenance of the front wheel during its mounting or removal.
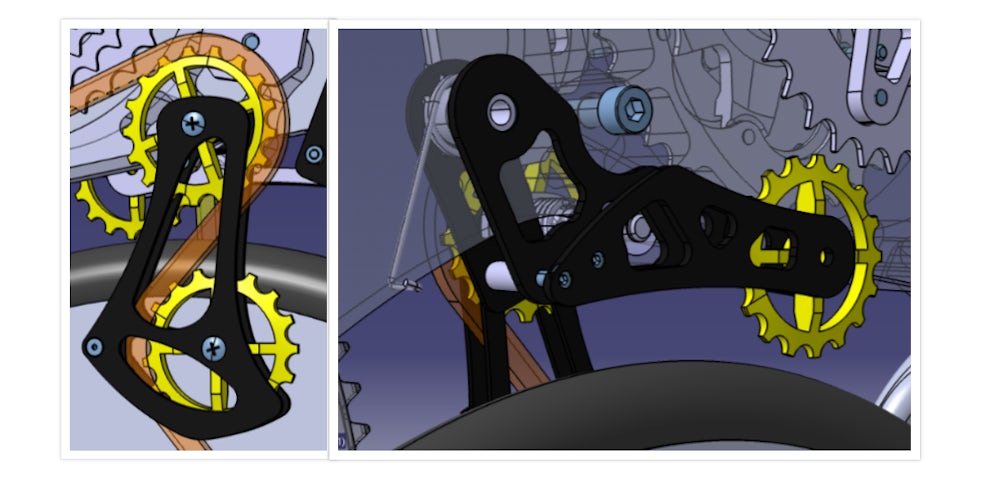
The servos of the V1.0
The axial movement of the cassette is managed by two powerful electromechanical servos, based on “coreless” motors that are able to create almost 2Nm of torque each.
With the connecting mechanism between the servos and the cassette, we can achieve about 20Kg of thrust. This enables the transmission to change gear very rapidly and precisely even if the cyclist is still applying power. The servos are powered by two lithium cells capable of generating 7.4V. The brain behind the shifting system is an Arduino Mega 2560, based on the Atmega2560. It interprets the signal coming from the two buttons on the steering handle and sends a command to the servos to correspondingly move the cassette.
The transmission V2.0
In 2017, the competition in BM brought new ideas on how to improve the transmission system.
The main points we focused on were:
- Weight of the system: since Taurus was quite heavy, the new goal was to make it as light as possible. The transmission system definitely needed to be improved. Aluminum and steel components were redesigned by removing material where it wasn’t needed and by using lighter materials, such as plastics and carbon fiber, where possible. We also managed to change many commercial components, for example the chain and the pinions, with more advanced and lighter ones. We decided to buy an ultra-light chain and to make a new carbon fiber chainring. Overall, we removed almost 1.6 Kg of weight. That means less inertial mass and less weight on the wheels, therefore less drag due to rolling resistance.
- Functionality: the old action used a crank-rod mechanism that imposes a nonlinear movement to the cassette, making calibration harder. This problem was solved by using a different mechanism: rack and pinion system.
- Efficiency: even if the chosen transmission system is intrinsically efficient, we tried to maximize its efficiency even further with a deeper study of the chain and lubricant.
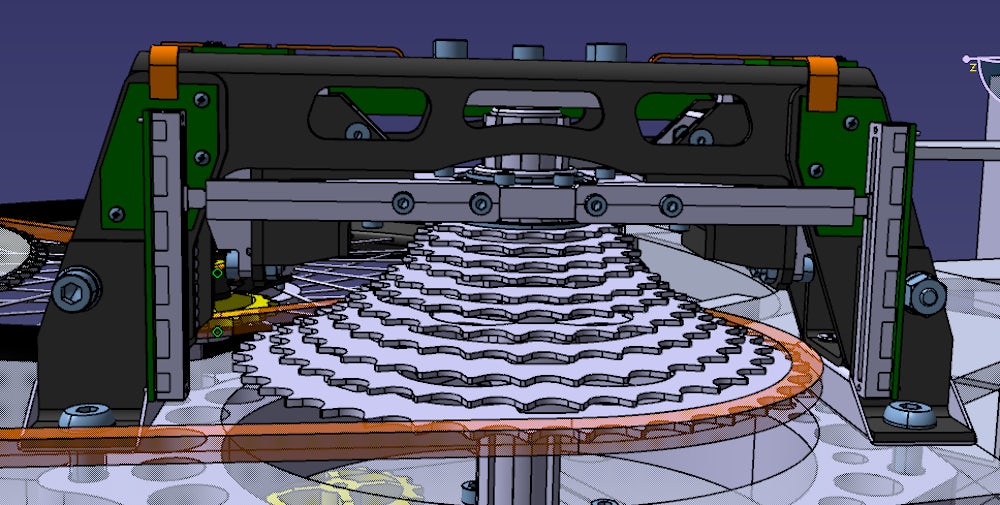
The improved system presents a splined shaft holder (the bridge like structure) which is more compact and lighter than its predecessor. In the picture you may notice the complete carbon fiber structure.
The new system has been tested during the competition in BM of 2018. It works precisely and rapidly and it doesn’t seem to require further modification. The only problem was that the chain could not perfectly engage the correct gear when working on the higher pinions. In that part of the cassette, the pinions have similar diameters: this caused the chain to jump over two gears. This problem was solved by changing the geometry of the right tensioner. The new shape brings the pulleys closer to the cassette when the chain is on the higher gears.
The development of this technology brought three members of the team to register two patents, which in the future could even be implemented into the industrial production of high-end bikes characterised for high performances and efficiency.
Conclusions and ideas for the future
Even though the actual transmission is very efficient, it has the disadvantage of having two chains because of the massive transmission ratio. The goal for the future is the development of a single chain transmission system. Though it would be quite a feat, it is not impossible.
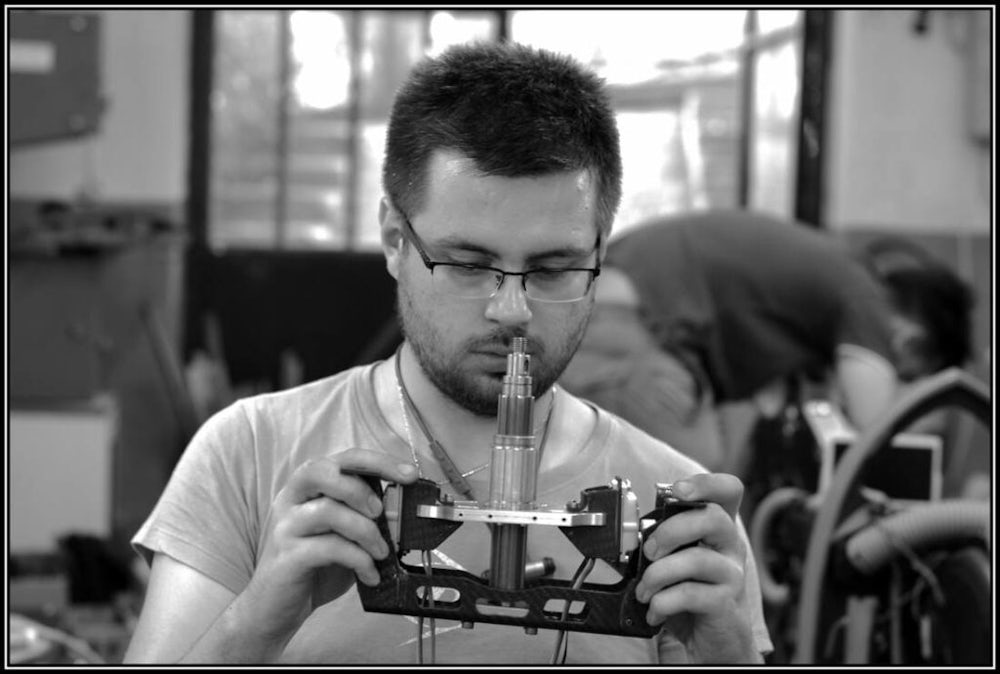
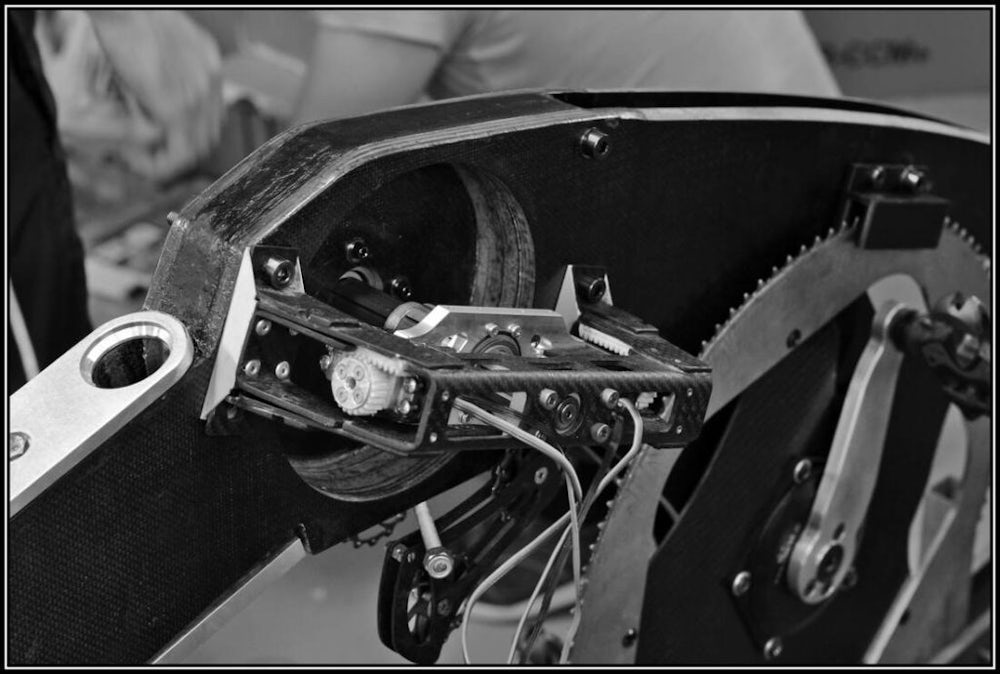
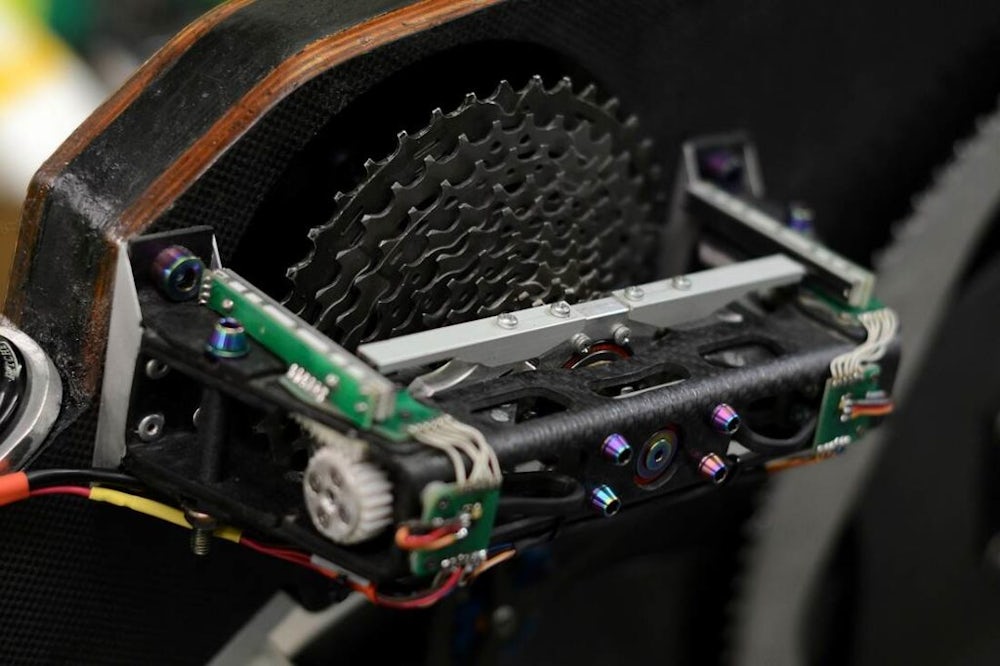
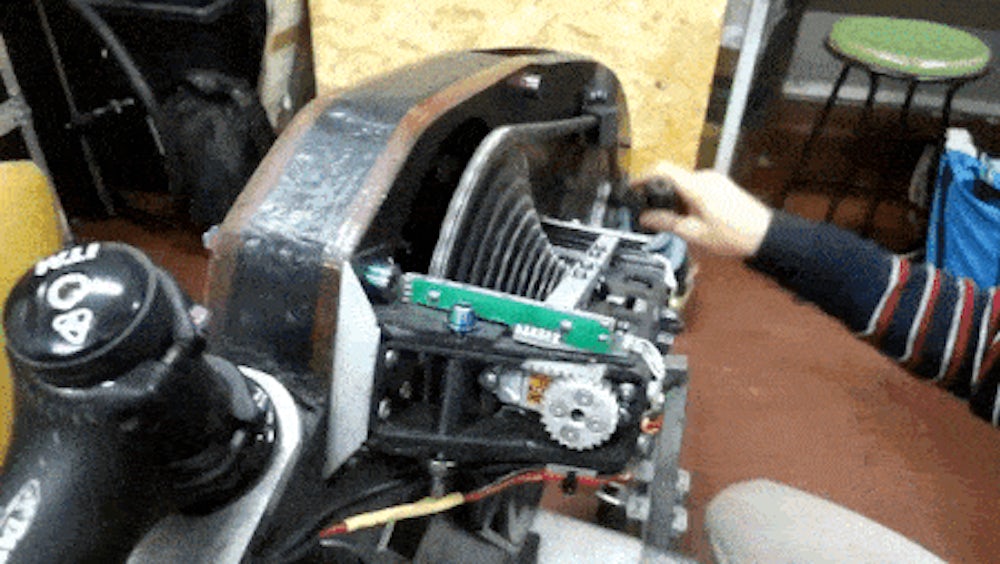